The search for adsorbents that can selectively remove CO2 from air encompasses a wide range of materials with different surface chemistry. We are developing nanoporous solids for this, where the very high internal surfaces can be exploited and the interactions readily tailored. In the contactor bed, with high input airflow through monoliths, good equilibrium uptake is required where the CO2 level is only 420 ppm. In addition, other important criteria must be met in this bed. These include fast kinetics of the CO2 uptake and easy desorption at moderate temperatures, and furthermore the uptake should not be too strongly affected by the presence of some moisture in the air stream. These stringent requirements, which we in SOLDAC check can be met, restrict the number of suitable materials to some key candidates. Additionally, once the CO2 has been captured, there is a requirement to concentrate it further in subsequent beds.
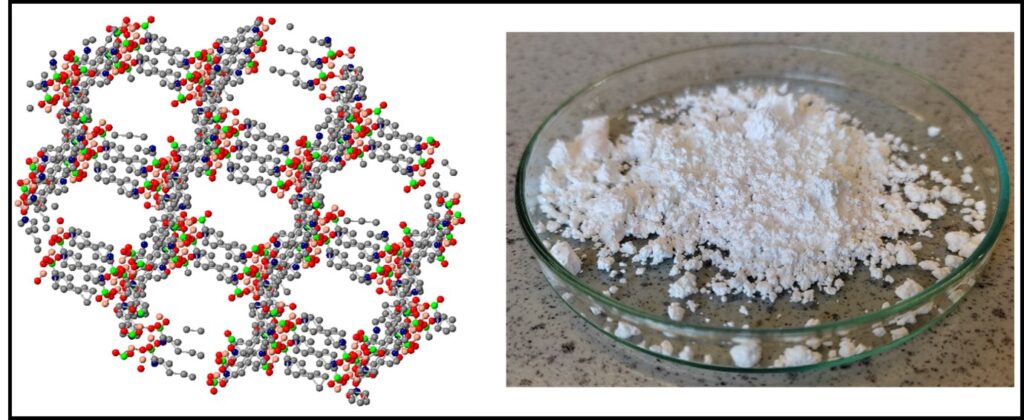
After careful selection of promising nanoporous materials for the overall process, including metal organic frameworks (MOFs) and inorganic zeolites, the next step is to fabricate these materials in forms appropriate to their role in the DAC unit. This involves wash-coating microcrystalline powders with good consistency onto a monolith support or shaping the powdered materials into pellets using binder additives. The pellets can then be used for adsorption beds, where they will not build up appreciable back pressure when gases flow through them. In each case, our workflow must provide confirmation that the materials retain their adsorbent properties after their application as coatings or when in pellet form.
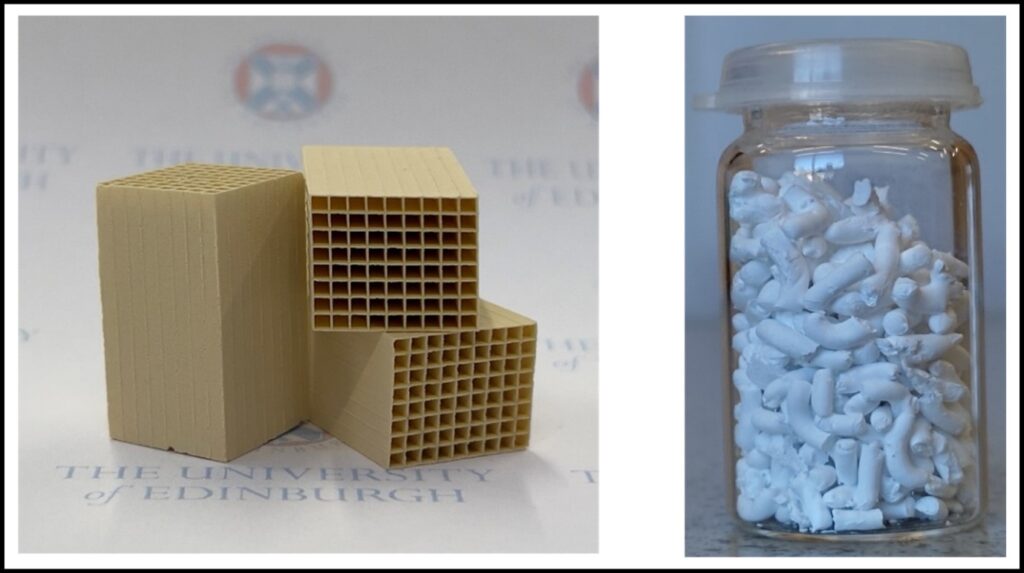
Written by Harpreet Kaur and Paul Wright, St Andrews University